Implementing Virtual Reality into Footwear Design
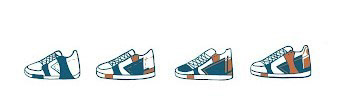
Introduction
Extended Reality is nothing new in the world of gaming and immersive experiences. For over two decades, consumers have been able to transport themselves from the physical world using Virtual Reality (VR).
Extended reality has played a large role in consumerism and continues to allow for mass customization of products [4]. Magnolia, a home decor brand, has created an Augmented Reality (AR) experience for consumers in an app called Magnolia Market. This app enables the consumer to choose an object, such as a vase, and to virtually see it in their space before purchase [1].
Footwear Development
When footwear development began to take off in the 1970s, scientists focused solely on the mechanical forces coming from the shoe rather than how the foot would interact with these forces. As the field of footwear development continued to evolve, scientists began to consider biological and sensory reactions while wearing the shoe [3]. The comfort of the user was as important as the shoe's performance. Another aspect of footwear that scientists began to pay attention to was the aesthetic appeal [2]. The shoe had to look good and function well.
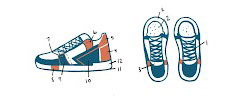
Figure 1
Parts of a Sneaker
1. Mudguard 7. Lower Tongue
2. Vamp 8. Midsole Accent
3. Tongue 9. Lower Eyestay
4. Lower Heel 10. Varial/Medial Panel
5. Upper Heel 11. Outer Sole
6. Upper Eyestay 12. Midsole
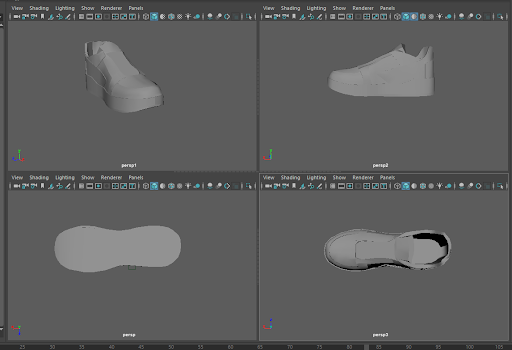
Figure 2
Development
After creating a sketch for the silhouette of the shoe, it was modeled in Autodesk Maya (Fig. 2). Each component of the shoe was created as an independent object to allow for customization later.
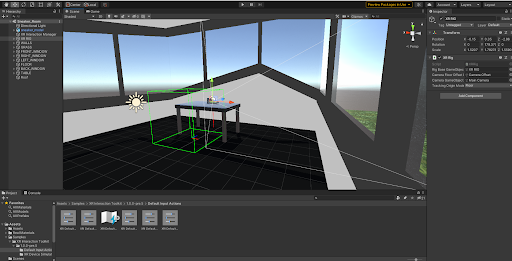
Figure 3
Virtual Studio in Unity
A simple design studio (Fig. 3). was created in Unity for the sneaker model to be modified in. To allow for user input/interaction in virtual reality, a VR Rig was added. This controls the user’s view and controllers.
Adding Functionality
Virtual hands (Fig. 4) with realistic physics were later added for a hands-on feel. The triggers on the controllers control the movement of the fingers and allow the user to grab and interact with the shoe.
The resulting program allows the user to interact with the 3D model of the shoe and have a full 360 view at all times (Fig 5). The physics on the hands corresponds with the user’s interaction with the controller.
With the implementation of the user interface (UI), the shoe’s material type and color can be modified through the buttons on the screen (Fig. 6). The matte or patent will change the appearance of the panel, while the buttons along the right will change the color.
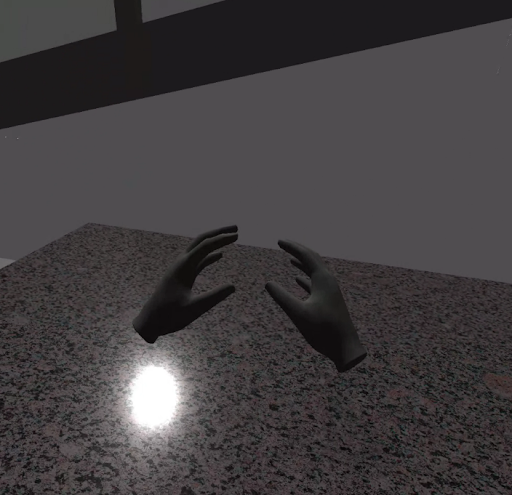
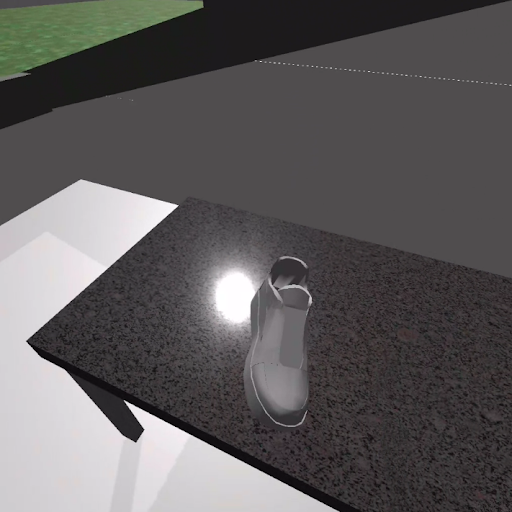
Conclusion
As companies try to make products more widely accessible through technology, virtual storefronts will become more common. Programs like this one will allow the consumer to create a product of their liking in the virtual space.
While this project is only a small prototype, the concept of designing a product in the virtual space and ordering it to be produced physically is the next step in fulfilling the needs of consumers.
Future work for this project may include expanding on the available shoe silhouettes. An augmented reality try-on might also be added for a better visual before manufacture. This program can be expanded upon to provide a better overall experience in mass customization.

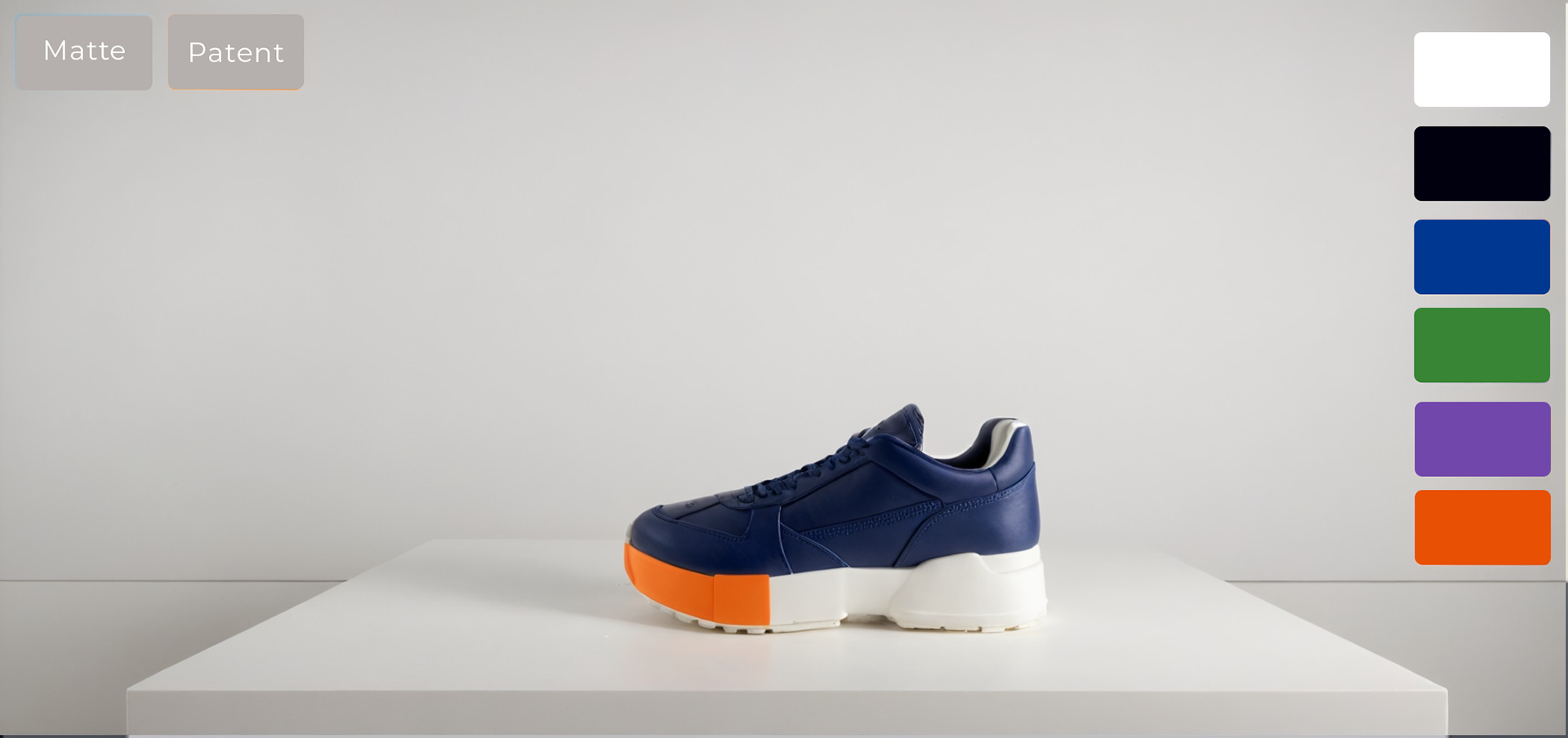
References
[1] Berni, Aurora; Borgianni, Yuri: Applications of virtual reality in engineering and product design: why, what, how, when, and where. 2020.
[2] Fralix, Michael T.: From Mass Production to Mass Customization. Journal of Textile and Apparel, Technology, and Management 2001.
[3] Nigg, Benno M.; Stefanyshyn, Darren J.; Cole, Gerald K.; Boyer, Kath: Footwear research – past, present, future. 2007.
[4] Novak, Boštjan; Fatur, Peter; Dolinsek, Slavko.: Mass customization in the footwear industry: A case study. 2007.
Acknowledgements
Thank you to The Gatton Academy and The Western Kentucky Sisterhood for the Research Internship Grant that funded this project. Thank you to Dr. Michael Galloway for his mentorship, and thanks to the other members of the XR Lab for their continuous support.